Dynamo Blog, March 5, 2020 Matt McHugh
Explaining the age-old problem around visibility and transparency
While digitalization matures, the movement of goods will still need better connective tissue to seamlessly move information and value across heterogenous global logistics platforms, particularly critical information such as bills of lading, certificates of origin, insurance verification, and invoicing. Even as EDI-based transactions digitalize many of these processes, there remains plenty of paper-based exchange. – Deloitte FoM Report
Detailing The Problem
Tracking solutions monitor goods on their journey through the supply chain, collecting freight data, and creating actionable insights based on that intelligence. Simply put, they capture data from an operation’s supply chain. This tracking data provides visibility of the particular supply chain’s organization and often manifests itself in questions like:
- Who has handled my freight?
- What is the environment like? (temperature, humidity, pressure, acceleration)
- What has the journey been to date?
- When is it supposed to arrive?
- Where is my shipment?
- Why were there issues? (if there were any)
- How do we remediate? (and proceed to take the necessary steps)
For most supply chains, these simple questions are difficult to answer consistently, with certainty, and with relative operational ease. The status quo is to conduct manual check-ins, validate data from imperfect tracking solutions (consider solutions that are delayed or are tracking the cab vs trailer or ship vs container), and query business systems. Most of this happens at checkpoints like warehouses, and real-time, in-transit visibility is just beginning to burgeon, ushered in by the likes of FourKites and project44.
Transparency, in this context, is when intra-organization or intra-node visibility data is shared with fellow stakeholders and adjacent nodes in a supply chain. 72% of supply chain professionals admit having no transparency with their suppliers below the second tier.This gap is meaningful to companies, not only because of regulatory scrutiny but also because more transparency means more customer trust and more sales. Validating this, in another survey, 75% of companies considered transparency helpful in strengthening trust between businesses and consumers. Today, the scope of transparency is limited because the requisite data is often difficult to gather, processed and analyzed manually, and exchanged via phone calls, emails, or fax machines.
The breadth of the supply chain involved also contributes to the nature of the problem. Are the logistics in-house or outsourced? Is it a closed-loop or open-loop supply chain? These factors may leave a company with more or less control over its shipments because there are more parties involved. The more parties involved, the more important visibility and transparency become, but the more difficult a solution is to implement, lowering ROI. On the flipside is an organization like Amazon, which takes advantage of its end-to-end logistics, IoT connected warehouses, and variety of last-mile partners to see across its growing network — marrying it all with AI applications to match shipments to the lowest cost collaborative parties. Controlling its supply chains end-to-end eliminates the need for granular IoT solutions in most cases. The company can just map packages to its network of drivers as a proxy to provide users with real-time location data. It’s only when sensor data becomes critical that item-level technology merits deployment.
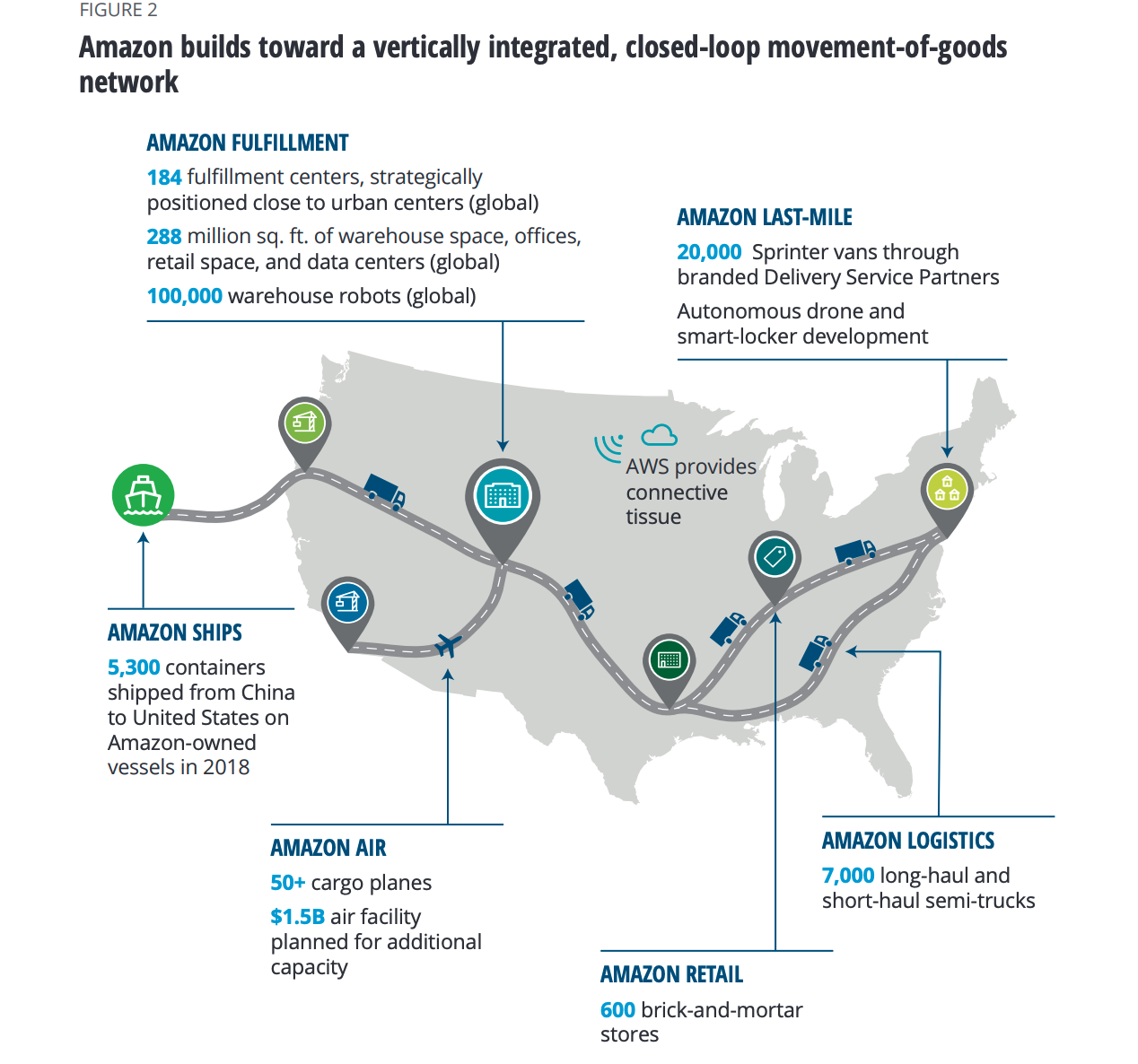
Examples Across Industries
A poultry processor is going to want to know if the temperature, humidity, and contamination controls on a shipment are being met as it goes from processing facility, through a distributor, to the end consumer on a series of trucks. Without this data, processors are helpless to prevent or assign accountability for costly product recalls and quality issues.
Similar problems arise around high-ticket items like pharmaceuticals. On top of temperature and humidity monitoring, the manufacturer is going to want to know that the shock and light levels are kept within acceptable limits by the carrier. There are exorbitant penalties for violating the regulations around the transportation of these materials. As little as a 2°C temperature variation could completely ruin the product, costing a pharmaceutical company $150,000 on average.
Even low-ticket items like consumer commodities are a point of concern when large quantities are being conveyed. Supply chains are impossible to optimize when logistics managers cannot triangulate bottlenecks and locate precisely where losses are occurring. At high enough volumes, these marginal inefficiencies represent large sums of value.
The Two-Minute Technology Primer
In understanding how physical goods are tracked, consideration must be given to the requisite sensors that capture and transmit data to software systems. This data includes location, temperature, pressure, humidity, speed, etc. The sensors are a means to an end with a mix of options to address capability, durability, and security. It’s worth noting that different supply chain environments will require different hardware solutions, given there is no “silver bullet IoT device” (this is a great opportunity for hardware-centric engineers). The selection of solutions is derived from a function of balancing these environmental limitations and cost considerations to best match the particular nature of the freight at hand.
The takeaway is that when it comes to picking the best device, the answer is a big, fat, unsatisfying—it all depends. Different devices are better for different use cases with varying cost and ROI considerations. Today, the resulting mix of devices creates fragmentation in the system. It’s also worth noting that sensor tags can be a substantial expense but the Internet of Things (IoT) cost curve is continuing to decrease. Microsoft’s recently released 2019 Manufacturing Trends Report found that the average price of an IoT sensor has declined from $1.30 in 2004 to $0.44 in 2018, headed to $0.38 in 2020.
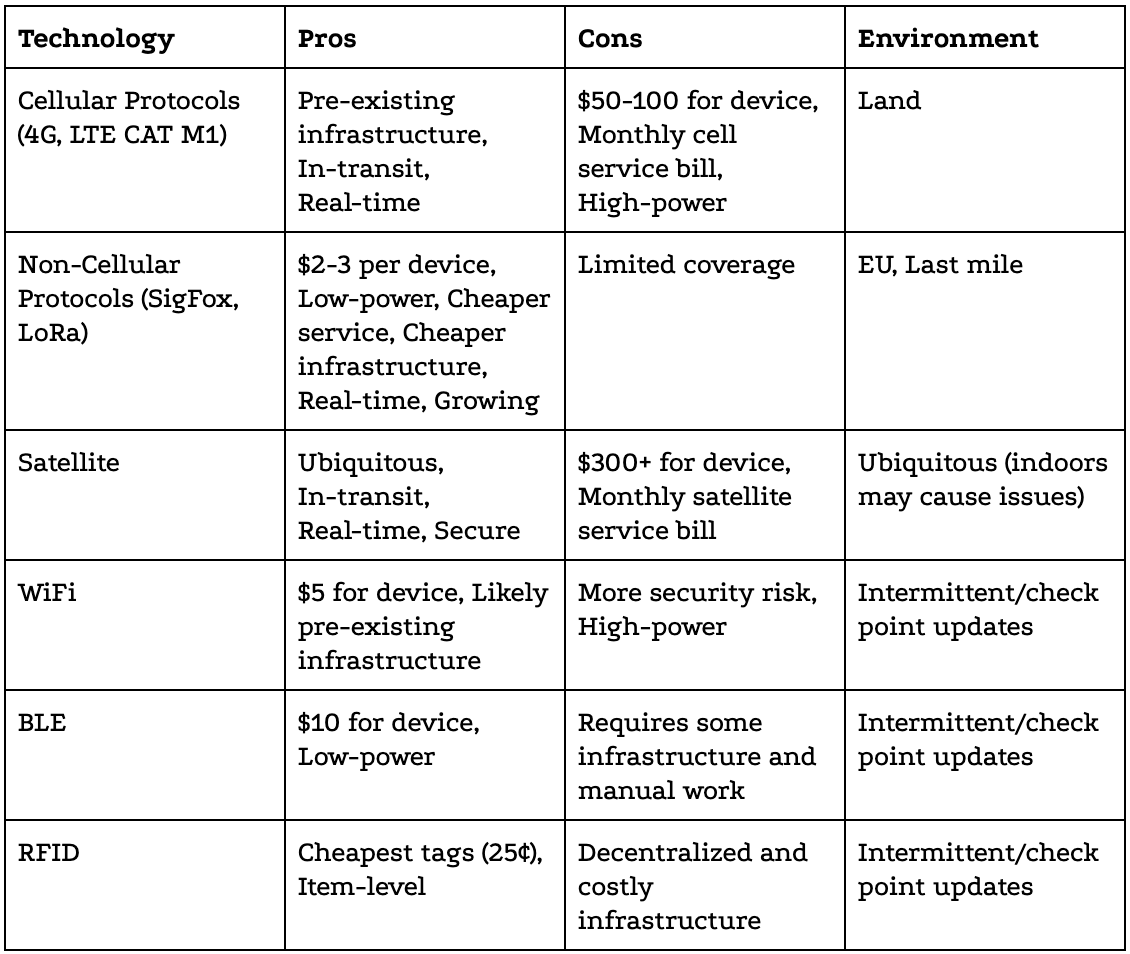
All Roads Lead To Rome
Like most problems, there are many ways to solve this problem, and our conversations with prospective customers and solution providers over the year distill to five key beliefs.
- The devices that track and transmit data are ultimately a commodity despite being a bottleneck in the short term
- Track at the freight level wherever possible
- Cost matters but different supply chains have different ROI thresholds for the same problem
- Facilitating transparency among supply chain constituents is the status quo
- Value is built around the actionable insights and ability to drive process automation
Vertical-Specific Solutions
One of the elements of delivering great visibility and transparency is the vertical in question and nature of freight being tracked. The nature of freight determines the necessary processes and stakeholders needed for handling the freight. This informs the practicality of different solutions. Consider the aforementioned examples: perishable food products, pharmaceuticals, and consumer commodities. Each is handled very differently, which has an impact on the type of data to track and transmit, the frequency the data is transmitted, and the willingness to pay for a solution.
We believe certain supply chains have enough complexity and value to warrant vertical-specific solutions. Some areas we think could be interesting include perishable foods, petrochemicals, and high-value electronics.
Environment-Specific Solutions
A second reality of supply chain is coping with the environment that freight passes through on a regular basis. The geography of a shipment usually introduces limitations around the ability to capture and transmit the requisite data. Consider a container on a ship steaming across the Pacific Ocean or an air freighter that’s flying from London to Memphis. Something that works on ocean containers might not work for freight transported by air. To further complicate matters, warehouses and ports tend to have poor connectivity, if they have any at all. It might seem that trucking is the bright spot of the global supply chain, but tracking is usually limited to the cab rather than the trailer or pallet. These dynamics force a conversation around acceptable limitations of a solution, hardware selection, and ultimately cost.
We believe certain areas of supply chain are still in need of basic telemetry including ocean ports, airports, and warehouses. Each of these segments is a major part of global trade. However, they are often dubbed “black holes” as they create visibility gaps in otherwise transparent supply chains.
Middleware + RPA Approach
There’s great value in creating a middleware that conforms with all the different devices, extracts data, and distills that data into actionable insights. There’s also ample opportunity for predictive analysis or scenario modeling to optimize areas of the supply chain. This will naturally lead to an opportunity to automate processes that leverage the understanding and experience of supply chain managers. In effect, such a solution handles the fragmentation of hardware that results from heterogeneous freight and varying environments. Only then, will the moving parts be brought together in a coherent way to control these problems and optimize contingency management.
Software is eating the supply chain and interoperability is the next rung in the ladder. When framed around our five key beliefs, the complexity of supply chain tracking is much easier to unpack. Once explicitly outlined, the constraints of different verticals and environments can be addressed accordingly, proving clarity around the best integration solutions. Proactive tailoring of these solutions and harmonized data will enable supply chain managers to get all their questions about the flow of their supply chains answered at the lowest cost possible. All said and done, supply chains will become increasingly prognostic, driven by holistic decisions, and configured to real-time demands.